The satisfying feeling of stepping into a brand-new pole barn is one many dream about. But for those who need a robust, durable floor for their workspace, the cost of concrete can be a major factor to consider. There’s a lot to think about: size, type of concrete, thickness, reinforcement, and finishing. This can be a confusing and overwhelming process, but don’t worry! We’ll guide you through everything you need to know about determining the cost of pouring your very own pole barn concrete floor.

Image: beehivebuildings.com
Before we dive in, let me share a personal anecdote. When I built my own pole barn workshop, I initially thought I could get away with a simple gravel floor. But after a few wet days, I quickly realized the need for concrete. I learned the hard way that a solid foundation is crucial for a long-lasting and functional workspace. It was an extra expense, but absolutely worth it in the long run.
Understanding the Costs
The cost to pour a concrete floor in a pole barn can vary significantly depending on several factors. Let’s break down the most important ones.
1. Size of the Floor
The square footage of your pole barn is the first and foremost factor in determining the cost. Larger floors obviously require more concrete, labor, and materials, driving up the total expense.
2. Concrete Type and Thickness
Different types of concrete have varying costs. Common types include:
- Standard Concrete: Most affordable, suitable for general use.
- High-Strength Concrete: More expensive but provides added durability and load-bearing capacity, ideal for heavy equipment or frequent vehicle traffic.
- Fiber Reinforced Concrete: Includes fibers for added strength and crack resistance.
The thickness of your concrete slab is another important consideration. Thicker slabs cost more but provide better strength and insulation.
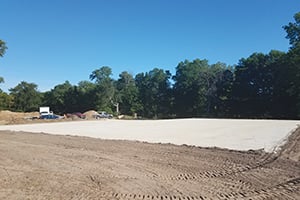
Image: info.fbibuildings.com
3. Reinforcement
Reinforcement, such as steel mesh or rebar, adds to the cost but is crucial for strength and preventing cracking. Use of reinforcement depends on the intended use of your pole barn. Heavy vehicles or machinery require more extensive reinforcement, whereas a storage space may not require any reinforcement at all.
4. Finishing
The type of finish you choose for your concrete floor can also influence the cost.
- Broomed finish: Most basic, textured finish, ideal for barns and garages.
- Smooth finish: Requires more labor, good for interior floors and easier to clean.
- Stamped finish: Decorative finish that mimics brick, stone, or tile, adds a high-end touch and a higher price tag.
5. Labor Costs
Labor costs are a significant portion of the total expense. Factors that influence labor cost include local market rates, the size and complexity of the pour, and the distance from your location to the concrete supplier.
6. Permits and Inspections
Depending on your local building codes, you may need to obtain permits and pass inspections for your concrete floor pour. These fees can add extra expense to your project.
Getting Estimates
The best way to get an accurate estimate for concrete flooring is to contact local concrete contractors. Ensure you provide them with:
- The size and dimensions of your pole barn
- The desired concrete type, thickness, and reinforcement
- The type of finish you want
Request detailed quotes from several contractors to compare pricing and service offerings. Read reviews and check online for contractor licenses and insurance.
Cost Savings
While it’s crucial to invest in a well-built concrete floor, there are ways to save money.
1. Choose the right concrete type and thickness
Don’t overspend on high-strength concrete if you only need basic strength. Consider factors like expected traffic and weight distribution when deciding on thickness.
2. Do some prep work yourself
If you’re handy, you can save money by prepping the site for the concrete pour yourself. This includes grading, setting forms, and laying gravel.
3. Compare contractor pricing
Request multiple quotes from different contractors to get the best possible price. You can also see if they offer discounts for seasonal or bulk orders.
FAQ
Q: How can I estimate the cost of concrete before contacting a contractor?
You can start with an online concrete calculator. While it won’t be precise, it’ll give you a general idea of the cost per square foot, based on concrete type and thickness.
Q: Do I need a permit for a concrete floor?
This depends on your local building codes. Check with your city or county’s building department for specific requirements.
Q: What is the best time of year to pour concrete?
Ideally, pour concrete in warmer weather, but not in extreme heat. Ideal temperatures for concrete curing are between 50 and 80 degrees Fahrenheit. Consult with a contractor about optimal pouring conditions for your location.
Cost To Pour Concrete Floor In Pole Barn
Conclusion
A concrete floor can be a significant investment for your pole barn but is a worthwhile one that will provide years of durability and functionality. By understanding the factors that influence cost and seeking quotes from reputable contractors, you can make a smart and informed decision for your pole barn. Make sure to consider your specific needs, budget, and local building regulations.
Are you planning to pour a concrete floor in your pole barn? Please share your thoughts and questions in the comments below.