Imagine a towering wall of shelves piled high with boxes, goods, and maybe even a fork lift truck driving between them. Now, imagine the whole thing tipping over. This isn’t just a scene from a disaster movie, it is a real hazard if racking isn’t properly secured. So, does racking need to be bolted to the floor? The short answer is, it usually does, and for good reason.
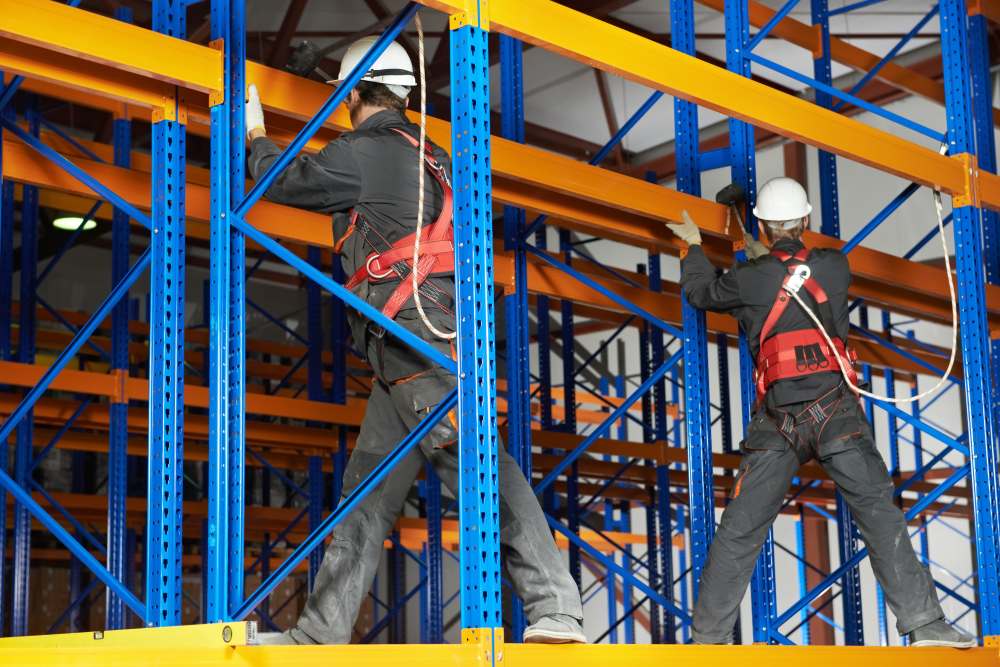
Image: betterstorage.com.au
The stability of your racking system directly affects the safety of the people working around it and the integrity of your inventory. Whether you’re running a warehouse, a retail store, or a small home office, ensuring your shelving units are secure is crucial. This article will delve into the reasons why bolting your racking to the floor is essential, explore the different types of racking systems, and provide practical tips for choosing the right anchoring solution for your needs.
Why Is Bolting Racking to the Floor So Important?
Racking systems, especially those that house heavy goods or are located in areas with high traffic, are susceptible to tipping and collapsing. Here’s why bolting them to the floor is a crucial safety measure:
1. Preventing Tip-Overs:
The primary reason for bolting racking to the floor is to prevent tip-overs, a hazard that can cause serious injuries and damage. Imagine a forklift maneuvering through the aisle, or a careless bump from a pallet jack. Without proper anchoring, even a slight impact could cause the entire structure to topple over.
2. Minimizing Damage:
A tip-over can lead to significant damage to the racking itself, inventory being crushed, and even structural damage to the building itself. Bolting the racking to the floor ensures that it stays in place, minimizing the risk of these costly accidents.
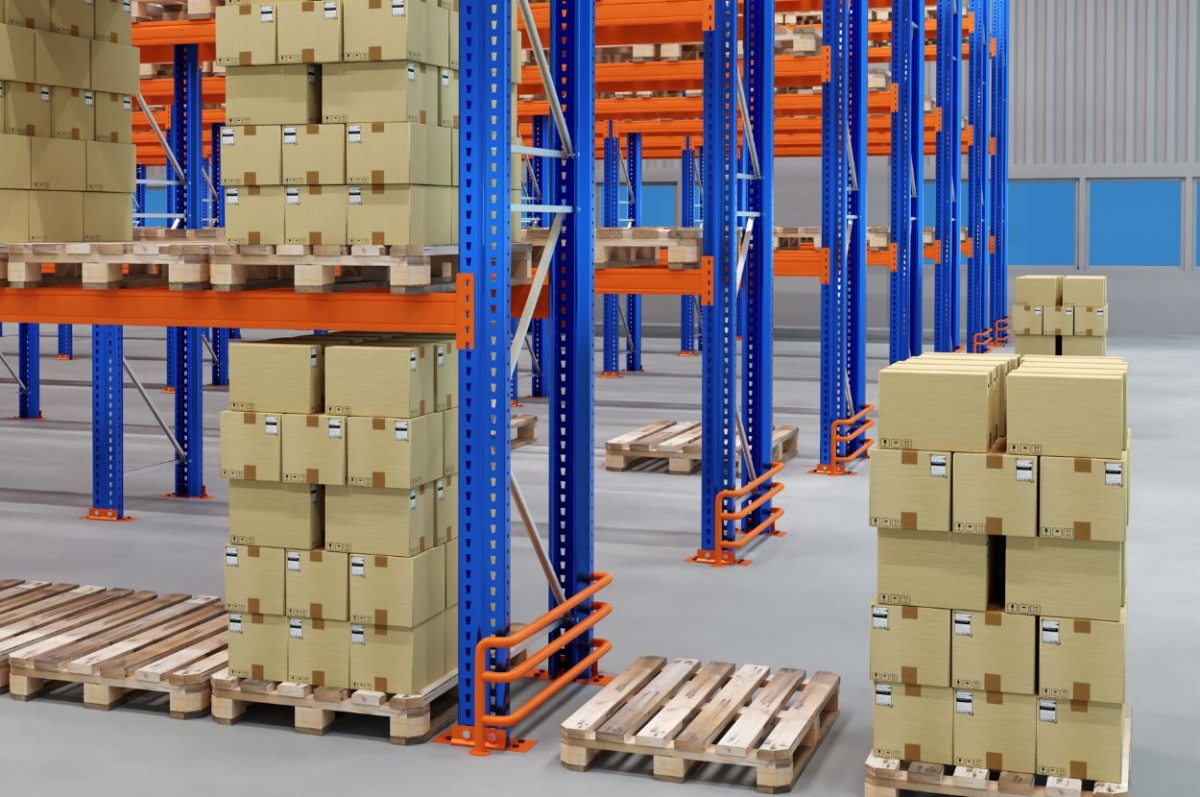
Image: racksafetyproducts.com
3. Meeting Safety Regulations:
Many regulatory bodies, including OSHA (the Occupational Safety and Health Administration) in the United States, require that racking systems be secured to the floor to comply with safety standards. This is particularly important when dealing with heavy loads, high storage heights, or specialized materials.
Factors Affecting Racking Security
Not all racking systems require the same level of stability. Several factors influence the decision on whether to anchor your racking:
1. Load Capacity:
The weight of the goods stored on the racking is a primary factor. Heavier loads require more robust racking and, in most cases, bolting to the floor. Lighter items, like stationery or books, may be safe without anchoring, but it’s always a good idea to consult with a professional.
2. Racking Height:
Taller racking systems are more prone to tipping, especially if they are loaded with heavy items. Higher structures typically require bolting for increased stability.
3. Location and Environment:
The location of the racking and the surrounding environment also play a role. High-traffic areas, areas prone to vibrations, or areas with uneven floors are more likely to require bolting. If your racking is situated in an earthquake-prone region, anchoring is crucial to prevent damage.
4. Type of Racking:
The type of racking system used impacts its stability. Some racking types, such as pallet racking and cantilevered racking, are more likely to require bolting compared to lighter-duty shelving systems.
Types of Racking Systems
There are numerous types of racking systems available, each with its own characteristics. Understanding the various types can help you determine the best option for your needs and whether bolting is necessary.
1. Pallet Racking:
Pallet racking systems are designed for storage of large quantities of palletized goods. These systems often require bolting because of the high load capacities and potential for forklift movement. They come in various configurations, including:
- Selective Pallet Racking: This type allows access to any pallet individually making it suitable for quick picking of items.
- Drive-In/Drive-Through Pallet Racking: This system stores pallets in a single depth, usually with a forklift traveling through the racking sections. Because of the high density, drive-in racking systems often require bolting.
- Push-Back Pallet Racking: This system utilizes carts that are pushed back to the rear of the racking, allowing for greater storage density, and typically requires bolting for stability.
2. Cantilever Racking:
Cantilever racking systems are ideal for long and bulky goods. These systems often require bolting to the floor due to the weight and size of the items stored.
3. Shelving Systems:
These systems are typically designed for lighter weight items and may not always require bolting. However, factors like load capacity, height, and the type of shelving system can influence the need for bolting. Here are some common shelving systems:
- Heavy Duty Shelving: Often found in warehouses and workshops, this type of shelving is made for heavier items and may benefit from bolting for greater stability.
- Light Duty Shelving: This type of shelving is typically used for home offices and retail stores and often doesn’t require bolting.
- Retail Shelving: This is a less heavy-duty version of shelving used for retail environments and usually doesn’t require bolting to the floor.
4. Mezzanine Systems:
Mezzanine systems create extra storage space within an existing warehouse. These systems typically require strong structural support and bolting to the floor because they are often used to store heavy items. .
Choosing the Right Anchoring System
If you decide that bolting your racking to the floor is necessary, you’ll need to choose the appropriate anchoring system. Here are some common options:
1. Floor Anchors:
Floor anchors are typically made of steel and are designed to be embedded into the concrete floor. They come in various sizes and configurations to accommodate the specific requirements of your racking system.
2. Chemical Anchors:
Chemical anchors are epoxy-based substances that are injected into pre-drilled holes in the floor. They harden to create a strong bond between the anchor and the concrete.
3. Concrete Screws:
Concrete screws are similar to traditional screws, but they have a special design that enables them to penetrate concrete without pre-drilling. They are often used for lighter-duty applications where the load or the racking height is relatively low.
4. Expansion Anchors:
Expansion anchors work by expanding within a hole in the concrete, creating a secure hold. They are often used for heavier loads and come in a variety of sizes and materials.
Professional Installation and Regular Inspections
While the information presented here provides a good understanding of why and how to secure your racking, it is highly recommended to seek the services of a qualified professional for the installation of your racking system. These experts have the expertise to ensure the proper anchoring system is chosen and implemented correctly for your specific needs and compliance with safety regulations.
Beyond installation, regular inspections are essential to maintain the safety and integrity of your racking system. Here are some things to look for:
- Damaged or loose anchors
- Worn or cracked beams
- Corrosion or rust on the racking structure
- Signs of uneven settling or movement
- Overloading or misalignment of loads
If you notice any of these problems, contact a professional immediately to address the issue before a potentially costly and dangerous accident occurs.
Does Racking Need To Be Bolted To The Floor
Conclusion
Bolting your racking system to the floor is a crucial step in ensuring the safety of your workplace and the integrity of your inventory. Understanding the factors that influence the need for bolting, choosing the right anchoring system, and conducting regular inspections are essential for preventing accidents and promoting a safe working environment. By prioritizing safety and employing proper racking practices, you can create a secure and efficient workplace for everyone.